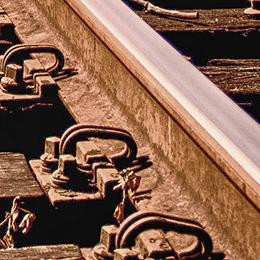
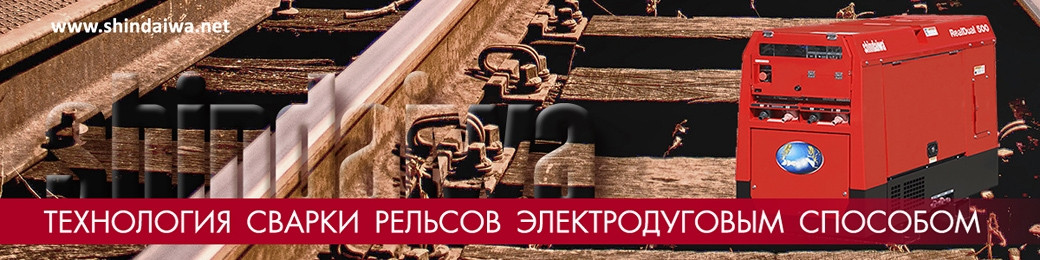
Зварювання рейок залізничних колій проводиться на постійному струмі покритими електродами або механізованим напівавтоматичним способом. Живлення здійснюється від електрозварювального устаткування (випрямляча, інвертора) або від спеціалізованих автономних дизельних зварювальних агрегатів (наприклад, Shindaiwa DGW500). Останні знаходять більш широке застосування через відсутність залежності від енергоносіїв і великого часу автономної роботи без дозаправлення.
Для зварювання рейок використовують електроди різних марок (зокрема УОНИ 13/55А, УОНИ 13/85), а також дріт суцільного перетину або порошковий газозахисний/самозахисний дріт з часовим опором наплавленого металу згідно з нормами і ДСТами.
Підготування рейок до зварювання.
Складення стиків залізничних колій під зварювання, як правило, здійснюють на шпалах. Кінці рейок обрізають по косинцю механічними засобами або газо-полум'яним способом. Після обрізання газо-полум'яним способом торці рейок необхідно очистити від окалини, краї – зачистити до металевого блиску.
Стик повинен бути вивірений у вертикальній і горизонтальній площинах, після чого він піднімається на 1,0-1,5 мм на 1 погонний метр.
Регулювання величини підйому стику здійснюють дерев'яними клинами, а перевірку — спеціальною сталевою метровою лінійкою з регульованими по довжині штифтами на кінцях.
Зазор між рейками, що зварюються, повинен бути 12-15 мм або 1,5 діаметра електрода з урахуванням товщини шару обмазки. Зварювання здійснюють на струмах 200-350 А.
Технологія зварювання рейок.
Технологічно зварювання рейкового стику залізничних колій можна розділити на дві основні операції: зварювання підошви, зварювання шийки та головки.
Зварювання підошви виконують на пластинці, що залишається (сталевий), або мідній, що знімається. Довжина цієї пластинки на 20 мм більше ширини підошви рейки, а ширина пластинки 40 мм.
Використовується кілька варіантів таких пластинок:
- Сталева (марка Ст. 3), товщиною 5-6 мм, пластинку укладають під стик і щільно підтискають.
- Комбінована, під стик укладають сталеву пластинку товщиною 2 мм, а під неї мідну підкладку.
- Керамічна підкладка з канавкою, що підтискається безпосередньо під стик.
Кращі результати дає застосування керамічної і комбінованої пластинок.
Підошва рейок – найбільш чутливе місце зварного стику, де особливо яскраво проявляються низька якість наплавленого металу та інші похибки зварювання.
При ванному способі зварювання рейок дуже важливо утримати у міжстиковому зазорі рідкий наплавлений метал і шлак. Для цього застосовують спеціальні мідні і керамічні форми багаторазового користування: нижні – для зварювання підошви і бічні – для зварювання шийки та головки.
Зовні форми мають прямокутну конфігурацію. Внутрішній контур їх відповідає формі тієї ділянки рейки, з якою вони сполучаються. По осі форми є виїмка, яка при зварюванні заповнюється рідким наплавленим металом з утворенням посилення стику.
При установленні форм їхню вісь поєднують із зазором стику, а бічні форми, крім того, ще й фіксують струбциною.
Зазор у місцях сполучення форм з поверхнею рейок не повинен перевищувати 1 мм. В іншому випадку краї форм необхідно обмазати вогнетривкої глиною.
Перед зварюванням стики рейок залізничних колій розігрівають газовими різаками або індукційним обладнанням до температури 400 градусів на довжину близько 100 мм від краю стику.
Зварюючи підошву, шов починають від краю пластинки і, здійснюючи коливальні рухи поперек зазору стику, ведуть його до іншого кінця, ретельно проварюючи кути між торцями рейок і платівкою. Другий шов слід накладати у протилежному напрямку, починаючи його також від краю пластинки.
При виконанні наступних проходів потрібно уважно спостерігати за тим, щоб рідка ванна розплавленого металу розташовувалася по всій довжині підошви.
У процесі зварювання коливальні рухи електродом потрібно здійснювати швидко. Закінчити зварювання підошви слід у центрі стику, завдяки чому шов виходить з ухилом від центру до країв, що відповідає профілю рейок. У підошві стику зварний шов повинен мати посилення у 2-3 мм, а краї підошви – перекриватися плавним швом. Поверхню шва після заварювання підошви потрібно очистити від шлаку.
Після установлення бічних форм слід негайно починати подальше зварювання, щоб не допустити значного охолодження стику рейок.
Зварювальна дуга збуджується у місці закінчення зварювання підошви, тобто біля основи шийки, і ведеться, безперервно заповнюючи наплавленим металом весь зазор. При зварюванні рейок покритим електродом важливо досягти швидкої зміни електрода, або проводити зварювання у двохпостовому режимі, при якому зварювальники поперемінно змінюють один одного (див. двохпостові агрегати DGW500 и DGW400).
Закінчуючи зварювання стику, на поверхні кочення необхідно наплавить прибуткову частину товщиною 4-5 мм, яка компенсує усадку при кристалізації стику.
Після зварювання, коли стик ще має червоний колір, поверхню його слід ущільнити куванням. Якщо виявлені які-небудь дефекти, подальше підварення можна проводити при температурі стику не менше 300 °С.
Зварювання рейок залізничних колій електродуговим способом є одним з найпростіших і в той же час економічно вигідних способів. Електродуговий спосіб не вимагає додаткових витрат на газо-захисні суміші або інші компоненти, а також їх логістику.
Одним з кращих рішень у цій галузі, є застосування вищевказаного способу зварювання у комбінації з двопостовими дизельними зварювальними агрегатами SHINDAIWA DGW500DM або ЗАК DGW500-2S.
Автономність даних машин і рекордно низьке споживання палива (4,7 л/год у 2-х постовому режимі) може забезпечити роботу на віддалених ділянках при мінімальних витратах. Таке низьке споживання палива при високому навантаженні пов'язано із застосуванням двигунів KUBOTA, які є одними з найбільш економічних у світі.
Агрегати SHINDAIWA призначені для роботи як на жорсткій «CV» так і на падаючій «CC» вольт-амперній вихідній характеристиці (ВАХ). Причому з огляду на незалежні обмотки генератора, для кожного поста вибір типу ВАХ передбачений індивідуально з можливістю паралельної роботи постів на різних характеристиках. Це дозволяє одним постом здійснювати ручний-дуговий спосіб зварювання покритим електродом, а другим постом, паралельно, виконувати напівавтоматичний механізований спосіб зварювання MIG/MAG.
Таким чином, при зварюванні рейок ванним способом із застосуванням SHINDAIWA можна комбінувати відразу два процеси – MMA і GMAW/FCAW. Це дозволяє значно скоротити час виконання робіт за рахунок високої продуктивності процесу MIG/MAG, а також знизити ймовірність утворення дефектів.
Необхідно відзначити, що важливим параметром застосовуваного обладнання є система формування і контролю зварювального струму джерела. Тип вихідного випрямляча (регулятора) безпосередньо впливає на якість і час зварювання, особливо з огляду на високі значення сили струму. В агрегатах SHINDAIWA реалізовано одне з кращих схематичних рішень вузла випрямляча (регулятора), результатом якого є повна, 100 %-ва відсутність безструмових пауз, а також вкрай низьке значення теплових енергетичних утрат вузла випрямляча, який практично не нагрівається при максимальному струмовому навантаженні.
Таким чином, обладнання Shindaiwa може забезпечити високу стійкість до перегріву, безперервність роботи 24 годинної зміни при високих техніко-якісних вихідних характеристиках, необхідних для процесу електродугового зварення. Що буде істотною підмогою при ремонті / зварюванні рейок і виконанні подібних робіт.
Для наочності у статті використані фотоматеріали видання livejournal.com.