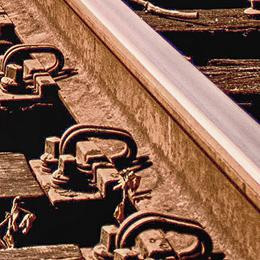
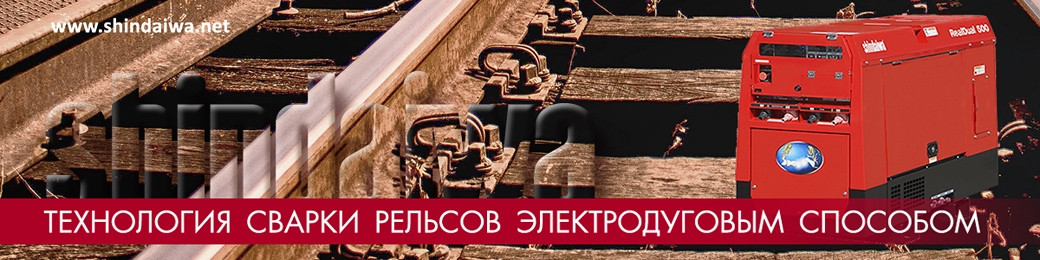
Сварка рельсов железнодорожных путей (ж/д путей) производится на постоянном токе покрытыми электродами либо механизированным полуавтоматическим способом. Питание осуществляется от электросварочного оборудования (выпрямителя, инвертора) или от специализированных автономных дизельных сварочных агрегатов (например, Shindaiwa DGW500). Последние находят более широкое применение ввиду отсутствия зависимости от энергоносителей и большого времени автономной работы без дозаправки.
Для сварки рельсов используют электроды различных марок (в частности УОНИ 13/55А, УОНИ 13/85), а также проволоку сплошного сечения либо порошковую газозащитную/самозащитную проволоку с временным сопротивлением наплавленного металла согласно нормам и ГОСТам.
Подготовка рельсов к сварке.
Сборку стыков ж/д путей под сварку, как правило, производят на шпалах. Концы рельсов обрезают по угольнику механическими средствами или газо-пламенным способом. После обрезки газо-пламенным способом торцы рельсов необходимо очистить от окалины, края – зачистить до металлического блеска.
Стык должен быть выверен в вертикальной и горизонтальной плоскостях, после чего он возвышается на 1,0-1,5 мм на 1 погонный метр.
Регулировку величины подъема стыка производят деревянными клиньями, а проверку — специальной стальной метровой линейкой с регулируемыми по длине штифтами на концах.
Зазор между свариваемыми рельсами должен быть 12-15 мм или 1,5 диаметра электрода с учетом толщины слоя обмазки. Сварку производят на токах 200-350 А.
Технология сварки рельсов.
Технологически сварку рельсового стыка ж/д пути можно разделить на две главные операции: сварку подошвы, сварку шейки и головки.
Сварку подошвы производят на остающейся (стальной) или съемной медной пластинке. Длина этой пластинки на 20 мм больше ширины подошвы рельса, а ширина пластинки 40 мм.
Используется несколько вариантов таких пластинок:
- Стальная (марка Ст. 3), толщиной 5-6 мм, пластинку укладывают под стык и плотно поджимают.
- Комбинированная, под стык укладывают стальную пластинку толщиной 2 мм, а под нее медную подкладку.
- Керамическая подкладка с канавкой, поджимаемая непосредственно под стык.
Лучшие результаты дает применение керамической и комбинирован ной пластинок.
Подошва рельсов – наиболее чувствительное место сварного стыка, где особенно ярко проявляются низкое качество наплавленного металла и другие погрешности сварки.
При ванном способе сварки рельсов очень важно удержать в межстыковом зазоре жидкий наплавленный металл и шлак. Для этого применяют специальные медные и керамические формы многократного пользования: нижние — для сварки подошвы и боковые — для сварки шейки и головки.
Снаружи формы имеют прямоугольную конфигурацию. Внутренний контур их соответствует форме того участка рельса, с которым они сопрягаются. По оси формы имеется выемка, которая при сварке заполняется жидким наплавленным металлом с образованием усиления стыка.
При установке форм их ось совмещают с зазором стыка, а боковые формы, кроме того, еще и фиксируют струбциной.
Зазор в местах сопряжения форм с поверхностью рельсов не должен превышать 1 мм. В противном случае края форм необходимо обмазать огнеупорной глиной.
Перед сваркой стыки рельсов ж/д путей разогревают газовыми резаками или индукционным оборудованием до температуры 400 градусов на длину около 100 мм от края стыка.
Сваривая подошву, шов начинают от края пластинки и, совершая колебательные движения поперек зазора стыка, ведут его к другому концу, тщательно проваривая углы между торцами рельсов и пластинкой. Второй шов следует накладывать в противоположном направлении, начиная его также от края пластинки.
При выполнении следующих проходов нужно внимательно наблюдать за тем, чтобы жидкая ванна расплавленного металла располагалась по всей длине подошвы.
В процессе сварки колебательные движения электродом нужно совершать быстро. Закончить сварку подошвы следует в центре стыка, благодаря чему шов получается с уклоном от центра к краям, что соответствует профилю рельсов. В подошве стыка сварной шов должен иметь усиление в 2—3 мм, а края подошвы — перекрываться плавным швом. Поверхность шва после заварки подошвы нужно очистить от шлака.
После установки боковых форм следует немедленно начинать последующую сварку, чтобы не допустить значительного охлаждения стыка рельсов.
Сварочная дуга возбуждается в месте окончания сварки подошвы, т. е. у основания шейки, и ведется, непрерывно заполняя наплавленным металлом весь зазор. При сварке рельс покрытым электродом важно достичь быстрой смены электрода, либо производить сварку в двухпостовом режиме, при котором сварщики попеременно меняют друг друга (см. двухпостовые агрегаты DGW500 и DGW400).
Заканчивая сварку стыка, на поверхности катания необходимо наплавить прибыльную часть толщиной 4—5 мм, которая компенсирует усадку при кристаллизации стыка.
После сварки, когда стык еще имеет красный цвет, поверхность его следует уплотнить ковкой. Если обнаружены какие-либо дефекты, последующую подварку можно производить при температуре стыка не менее 300 °С.
Сварка рельсов ж/д путей электродуговым способом является одним из самых простых и в тоже время экономически выгодных способов. Электродуговой способ не требует дополнительных затрат на газо-защитные смеси либо другие компоненты, а также их логистику.
Одним из лучших решений в этой области, является применение вышеуказанного способа сварки в комбинации с двухпостовыми дизельными сварочными агрегатами SHINDAIWA DGW500DM или САК DGW500-2S.
Автономность данных машин и рекордно низкое потребление топлива (4,7 л/час в 2-х постовом режиме) может обеспечить работу на удаленных участках при минимальных затратах. Такое низкое потребление топлива при высокой нагрузке связано с применением двигателей KUBOTA, которые являются одними из наиболее экономичных в мире.
Агрегаты SHINDAIWA предназначены для работы как на жесткой «CV» так и на падающей «CC» вольт-амперной выходной характеристике (ВАХ). Причем ввиду независимых обмоток генератора, для каждого поста выбор типа ВАХ предусмотрен индивидуально с возможностью параллельной работы постов на различных характеристиках. Это позволяет одним постом осуществлять ручной-дуговой способ сварки покрытым электродом, а вторым постом, параллельно, выполнять полуавтоматический механизированный способ сварки MIG/MAG.
Таким образом, при сварке рельсов ванным способом с применением SHINDAIWA можно комбинировать сразу два процесса – MMA и GMAW/FCAW. Это позволяет значительно сократить время выполнения работ за счет высокой производительности процесса MIG/MAG, а также снизить вероятность образования дефектов.
Необходимо отметить, что важным параметром применяемого оборудования является система формирования и контроля сварочного тока источника. Тип выходного выпрямителя (регулятора) напрямую влияет на качество и время сварки, особенно ввиду высоких значений силы тока. В агрегатах SHINDAIWA реализовано одно из лучших схематических решений узла выпрямителя (регулятора), результатом которого является полное, 100 %-ное отсутствие бестоковых пауз, а также крайне низкое значение тепловых энергетических потерь узла выпрямителя, который практически не нагревается при максимальной токовой нагрузке.
Таким образом, оборудование Shindaiwa может обеспечить высокую стойкость к перегреву, непрерывность работ 24 часовой смены при высоких технико-качественных выходных характеристиках, необходимых для процесса электродуговой сварки. Что будет существенным подспорьем при ремонте / сварке рельсов и выполнении подобных работ.
Для наглядности в статье использованы фотоматериалы издания livejournal.com.